Medical Device Package Testing
Medical device package testing uses a series of test standards to evaluate product and package safety in manufacturing, transit, storage, and in-use environments.
For over 30 years, Westpak has worked with medical device customers to help get their products to market. We start testing by collaborating with our customer; we discuss the product and package details, the distribution environment, the end-user, schedule, and any unique considerations that may influence the testing process.
Purpose of Medical Device Package Testing
The purpose of medical device package testing is to ensure products and/or packaging systems are safe and effective from manufacturing to transit and storage, all the way to the customer, which may be a surgical team in an operating room or a pharmacist at your local pharmacy.
Ultimately, these devices must meet the criteria set forth by ISO 11607-1, a consensus standard specifying the requirements for accelerated aging and sterile barrier testing of terminally sterilized medical devices:
- Accelerated aging tests are used to establish shelf life parameters by exposing the test sample to elevated temperatures, which rapidly simulate the effects of time on an object. This allows the manufacturer to compress the aging process, thereby speedily generating accurate test data to facilitate a shorter time to market.
- Sterile barrier integrity testing is used to evaluate the integrity of a medical device packaging system to ensure that production, transit, and storage do not compromise the sterility of the contents. The process involves several testing protocols, including, gross leak (bubble) testing, dye penetration testing, seal strength/peel test, and burst tests.
Medical Device Package Validation Tests
Medical device package validation incorporates package performance testing, accelerated aging, and sterile integrity testing following the guidelines of ISO 11607 -1 and -2. The repeatable testing available in a controlled laboratory lends a high degree of confidence in patient safety.
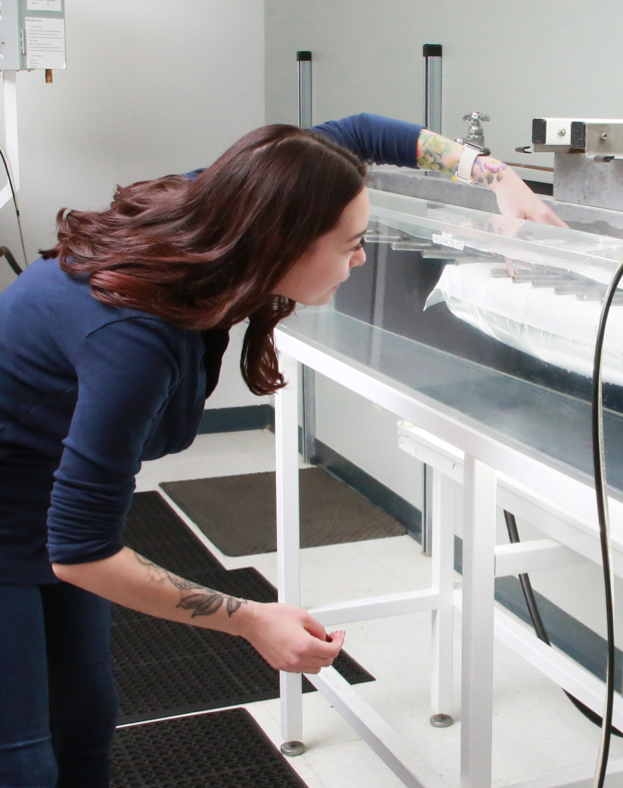
Westpak offers a variety of validated medical device package testing procedures for your needs. Our accredited laboratories are equipped to perform the following validated medical device package testing procedures:
Frequently Asked Questions
Get answers to our most frequently asked questions.
What requirements and standards do medical device packages need to meet?
Medical device packages are required to meet the two-part criteria outlined in ISO 11607. Part 1, Requirements for Materials, Sterile Barrier Systems, and Packaging Systems, and Part 2, Validation for Forming, Sealing, and Assembly Processes, are the two components of the standard.
For Part 1, a medical device package must meet the following requirements:
- Performance testing must conclude that the packaging system is able to protect its contents when exposed to hazardous conditions in handling, distribution, and storage environments.
- Package strength tests, such as seal strength (peel or burst testing), must demonstrate that the packaging system maintains its safety and effectiveness when exposed to mechanical forces.
- Package integrity tests, like dye penetration testing, must establish the sterility and integrity of the sterile barrier system until it is opened at the point of use.
- Stability testing (via accelerated and real-time aging) must demonstrate that the sterile barrier system remains intact throughout the expected shelf-life of the product.
Note: Pharmaceuticals sold in the United States must adhere to FDA packaging requirements set forth in Code 21CFR211.94.
For Part 1, a medical device package must meet the following requirements:
- Performance testing must conclude that the packaging system is able to protect its contents when exposed to hazardous conditions in handling, distribution, and storage environments.
- Package strength tests, such as seal strength (peel or burst testing), must demonstrate that the packaging system maintains its safety and effectiveness when exposed to mechanical forces.
- Package integrity tests, like dye penetration testing, must establish the sterility and integrity of the sterile barrier system until it is opened at the point of use.
- Stability testing (via accelerated and real-time aging) must demonstrate that the sterile barrier system remains intact throughout the expected shelf-life of the product.
Note: Pharmaceuticals sold in the United States must adhere to FDA packaging requirements set forth in Code 21CFR211.94.
How can I determine which medical device package tests I need to perform?
Medical device package validation incorporates package performance testing, accelerated aging, and sterile integrity testing following the guidelines of ISO 11607 -1 and -2. Many corporations will use a company-specific protocol to tie all these test inputs together, but you can also request them separately, according to your needs. Either way, Westpak is here to help. Westpak has the expertise to walk you through the test selection process as well generating a protocol if desired.
Accreditations:
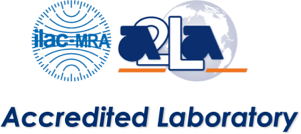
Testing at Westpak has been accredited by A2LA to comply with ISO 17025.
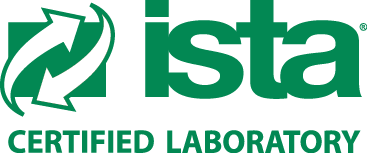
Westpak testing labs are ISTA certified to perform a variety of tests.