Distribution Testing
Distribution testing, often referred to as transit or shipping tests, is conducted on package systems to simulate the distribution environment.
Distribution Testing
When shipping products from one location to another, it’s essential to preserve the integrity of its internal contents until it reaches the end user. However, if those products are transported using insufficient packaging, significant problems can result. Damaged packages can result in sterile integrity breaches, product damage, and user bias upon shipment arrival. This will negatively impact valuable goods, rendering them unusable or lowering their value in the marketplace. Just a single shipment of damaged goods will not only lower profitability, but can also inflict lasting damage on a company’s reputation.
Optimizing packaging systems helps keep products safe as they go through its distribution environment from production to in-use, traveling from the manufacturing facility to the storage warehouse to the retail center, and ultimately to the end consumer. Not only does it offer safety, but optimizing a package will ensure that the package is not overpacked thus reducing both materials and supply chain costs. So how do you know whether your packaging system is optimized? Distribution testing is one of the best ways to put packaging systems to the test in order to gain a better understanding of their ruggedness and reliability. Read on to learn more about distribution testing, such as what it is, what it entails, and why it’s important.
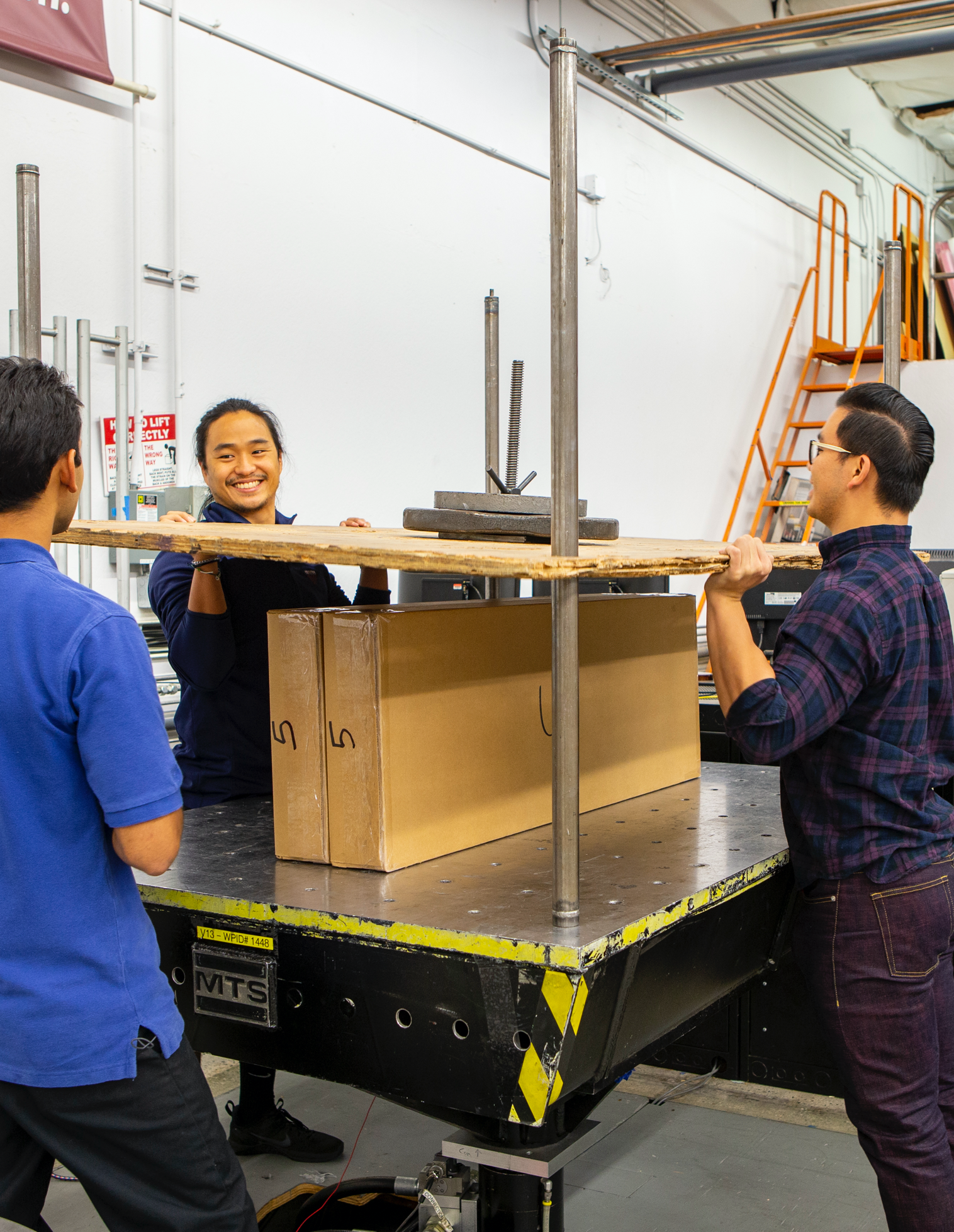
What is distribution testing?
Laboratory testing provides a controlled and repeatable setting where the ability of shipping units to withstand the distribution environment can be evaluated. This is accomplished by subjecting package test samples to a variety of tests such as impact, compression, vibration, environmental conditioning, and altitude. These tests replicate a significant portion of what the package will encounter in the actual distribution environment.
Achieving an optimized package system
To achieve an optimized protective packaging system, one must know the exact fragility of a product. The fragility of the product is defined as the point at which a product breaks from a specific test input. Certain products are more fragile than others when subjected to distribution inputs such as temperature, humidity, vibration, drops, and more. Product testing conducted in a laboratory can help to characterize the ruggedness of a product. Once this is determined, one of the best ways to determine if a package is optimized and resistant to damage is to test the packaged product in a controlled and repeatable laboratory setting.
Importance of distribution simulation testing
Every product needs to be sufficiently protected during its distribution environment. A shipment of damaged goods will hurt both profits and a company’s reputation.
However, an effective packaging system can protect products from damage and ensure they arrive at their destination safely.
One way to tell whether a packaging system is effective or not is to ship it through its actual distribution process, look for any weak spots or vulnerabilities, and adjust accordingly. However, subjecting packaging systems to the real-life distribution system is typically very expensive, time-consuming, and, overall, a wasteful endeavor. Plus, it’s impossible to replicate the same specific, repeatable and measurable results that are available in a laboratory setting with the appropriate sample size. Furthermore, depending on the regulations for your industry, these types of evaluations are ineligible to validate your package system.
This is where Westpak comes in: We evaluate packaging systems in our laboratory by subjecting them to tests that simulate the distribution process, from start to finish. We evaluate package performance and determine its integrity to establish how well the system will protect the product. Through controlled and repeatable laboratory testing, companies are able to gain valuable insights as to how they can optimize their packaging systems and keep their products safe throughout the distribution process. Finally, performing these types of distribution simulations is the only way to validate your package system when in a heavily regulated industry (such as medical and hazardous materials).
Frequently Asked Questions
Get answers to our most frequently asked questions.
What test methods can be used for distribution testing?
We make use of a wide range of methods when it comes to distribution testing. Some of the typical procedures and protocols we employ include:
- ASTM D4169: Standard practice for the performance testing of shipping containers and systems.
- ASTM D7386: Standard practice for performance testing of packages for single parcel delivery systems.
- ISTA 1A-3A: A diverse selection of tests developed by the International Safe Transit Association (ISTA), ranging from non-simulation tests to development tests.
- ISTA 1B-3B: Similar to the ‘A’ series, these tests are for unitized loads.
Distribution testing in a laboratory provides a controlled environment in which one can evaluate the package system’s ability to protect the product with repeatable and predictable test inputs. Performing a test suite such as ASTM D4169 or ISTA 2A ensures packaging systems are exposed to the many of the critical dangers, hazards, and disruptions they will likely face in the distribution cycle.
How does distribution testing simulate stresses normally encountered during package transportation?
Our laboratory uses cutting-edge test equipment and technology specifically designed to replicate conditions a package would face during transportation. Our tests simulate several factors that could cause damage during transit, such as environmental extremes (temperature, humidity, and altitude), impacts (drops), compression and vibration.
While we continually upgrade and expand our equipment capabilities, here are a few of our test asset types:
- Vibration test systems
- Compression test machines
- Drop testers
- Temperature and humidity test systems
- Altitude simulation test systems
- Incline impact test systems
What are the requirements of simulated distribution testing?
The overarching goal of simulated distribution testing is to optimize protective packaging systems, which in turn helps to ensure the safe passage of a product as it’s transported from the vendor to the customer. To achieve accurate results and efficiently optimize packaging, laboratory tests must follow industry guidance and testing standards.
Our team follows the industry standards set forth by organizations such as ASTM International and ISTA, which develop and publish guidance documents for package and materials testing. The standards developed by these organizations are used internationally by individuals, companies, and corporations alike. While requirements vary depending on the type of test that’s being performed, rest assured that our engineers wield a comprehensive understanding of the standards required for each test. By following widely-accepted and well-documented testing procedures, we’re able to produce high-quality results for clients working in a diverse array of industries.
Accreditations:
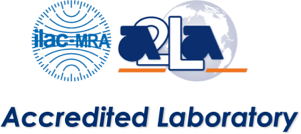
Testing at Westpak has been accredited by A2LA to comply with ISO 17025.
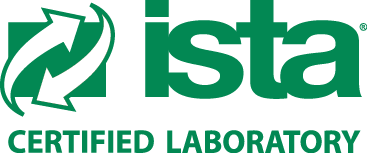
Westpak testing labs are ISTA certified to perform a variety of tests.