
Dangerous Goods Packaging Testing
Hazardous materials may require special handling and extra care. Westpak has the expertise and capability to handle HazMat package testing and analysis.
The shipment of hazardous materials has long been recognized as a potential problem area, conceivably creating significant harm to the general public if incorrectly or haphazardly conducted. To help correct this potential problem, the United Nations established guidelines for individual countries to adopt in order to make codified regulations similar throughout the world, thus initiating a “UN certified package”. In the United States, 49-CFR (Code of Federal Regulations) serves as the primary test protocols for “Hazmat” package testing.
The regulations resulted in procedures that require packages containing hazardous or dangerous goods to be subjected to Performance Oriented Package (POP) testing. This testing typically consists of a series or combination of impacts, stacking, vibration and pressure differential testing, among others.
To determine whether or not a product or material requires a UN certified package, one must first consult the 49-CFR standard to identify any requirements or special packaging instructions. Once it has been determined that a certified package is required, Westpak can assist in the process of providing the necessary testing and interpretation of the test results.
Conditioning
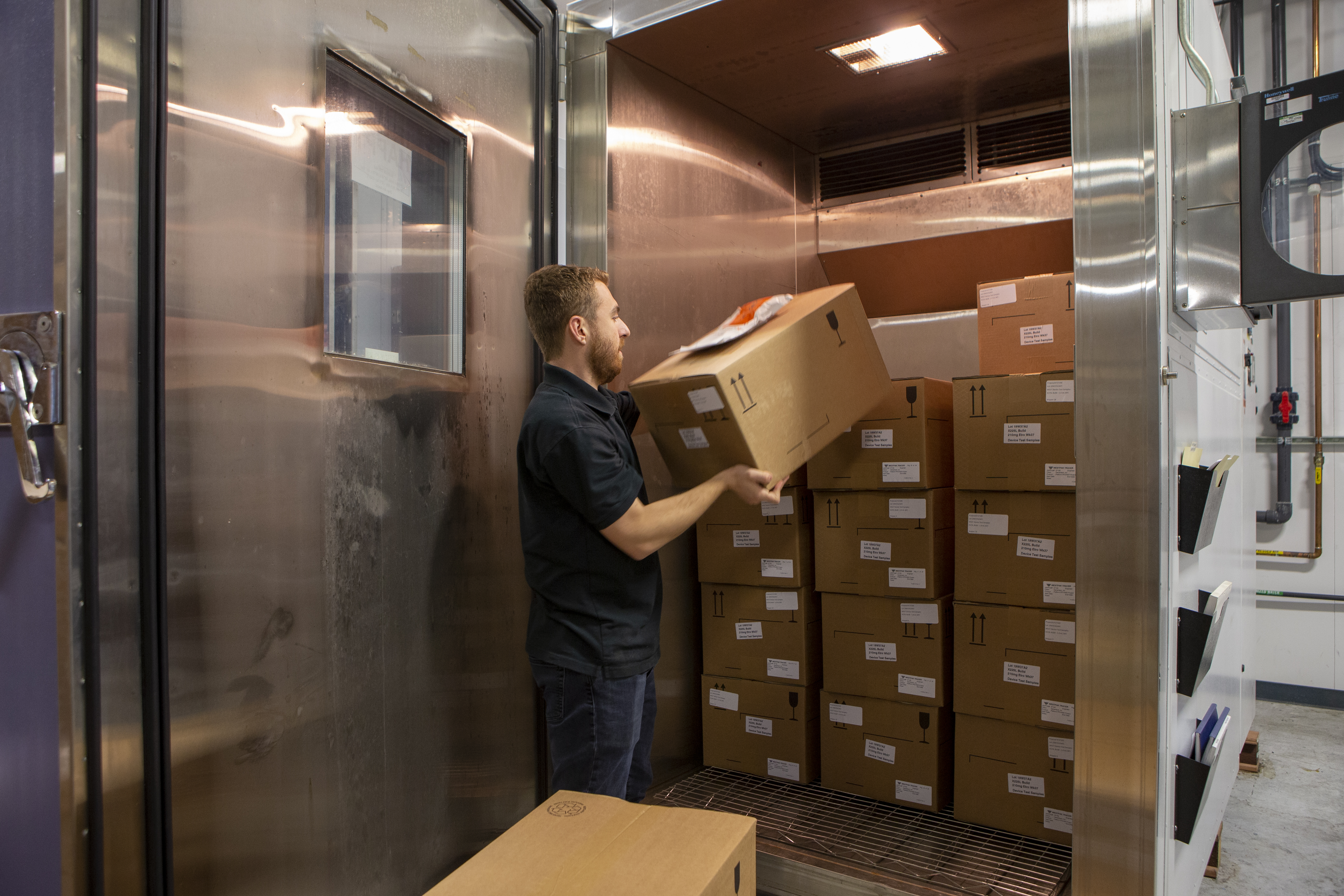
Conditioning
Environmental conditioning is a process of subjecting a test specimen to various temperature and humidity conditions in order to determine the effect of these conditions on the test specimen.
The testing is conducted in an environmental chamber designed to maintain tight controls over both temperature and humidity, as well as the rates at which these quantities are changed. The test levels chosen and the rates of change between these levels are often typical of what might be encountered during an extreme distribution cycle, for example, or storage for an extended period of time.
It is generally recognized that thermal stresses are some of the most severe that a product or package will be exposed to during its entire lifecycle. In addition, any hydroscopic elements of a product or package system will change their strength characteristics as they absorb or release moisture.
Typical Procedures/Protocols
49 CFR 178.602
49 CFR 178.603
WESTPAK Capabilities
Westpak continually upgrades and expands its equipment line-up. Therefore this list is a minimum of our capabilities:
(65)+ Temperature & Humidity Test Chambers
Drop
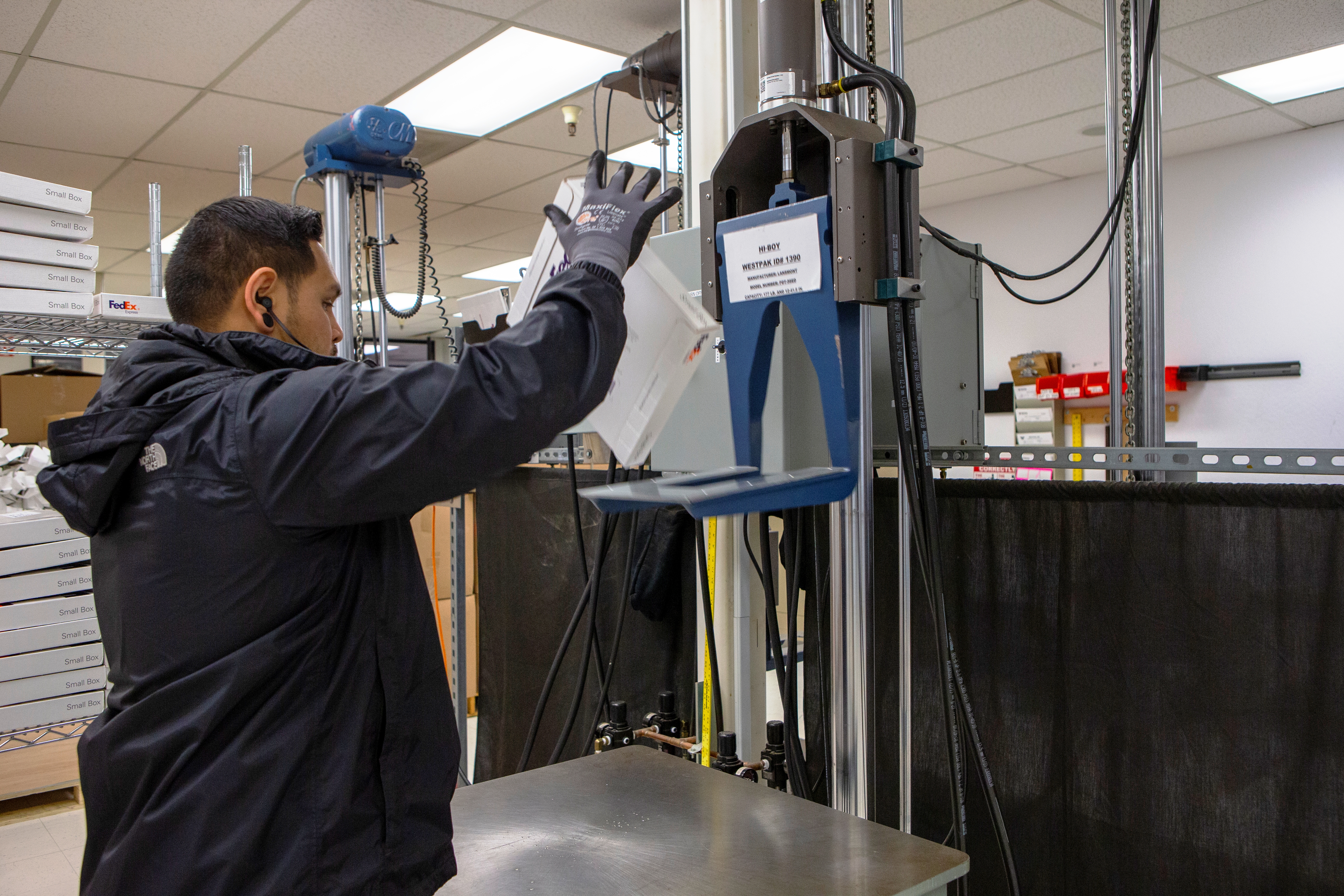
Drop
Just as the name implies, this test evaluates the ability of a package to handle and protect the product against collisions that occur in the distribution environment.
To conduct an impact test, the package is allowed to freefall onto corners, edges, and flat surfaces from a drop height dictated by the standard. Many test procedures conduct all of the impacts from the same drop height regardless of orientation.
Typical Procedures/Protocols
49 CFR 178.603
ASTM D 775
WESTPAK Capabilities
Westpak continually upgrades and expands its equipment line-up. Therefore this list is a minimum of our capabilities:
(8) Drop Testers
(8) Shock Test Machines
Stack
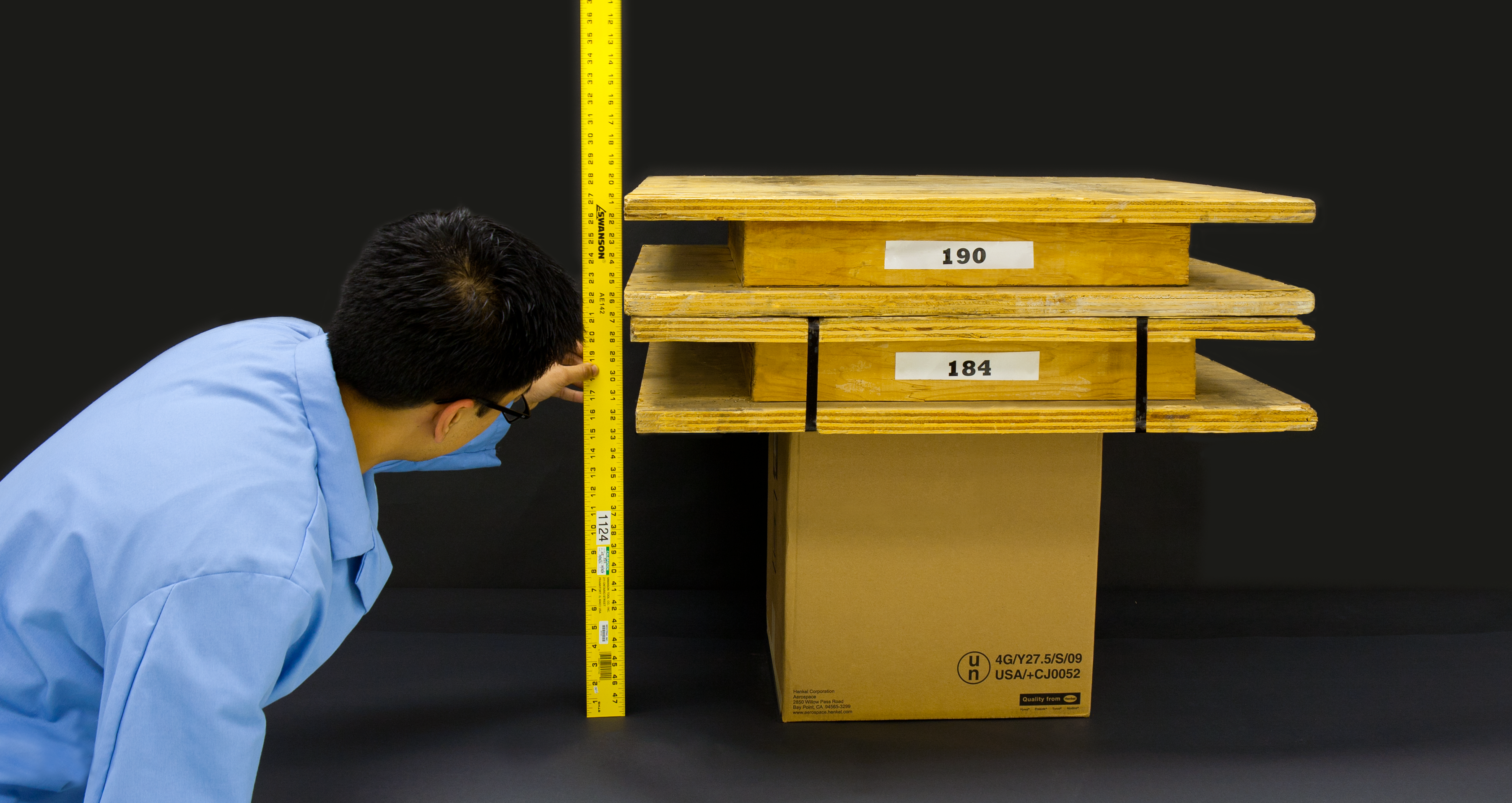
Stack
One of the primary functions of the container system is to provide the ability to stack the containers during transit or warehousing in a safe manner. This test simulates warehouse stacking hazards.
The stack test procedure requires that a dead load be placed on top of the package system that represents approximately 200% of the anticipated load during distribution. It must be a “free load” in order to lean if the stack should start to lean in any one direction. It is also necessary for the stack to maintain this level of top load for a minimum period of 24 hours. Westpak uses only certified loads calibrated yearly for this process.
Typical Procedures/Protocols
49-CFR 178.606
ASTM D642
WESTPAK Capabilities
Over 2250 Kg (5000 lb.) of calibrated dead load weights
(4) Container Compression Test Machines
Internal Pressure
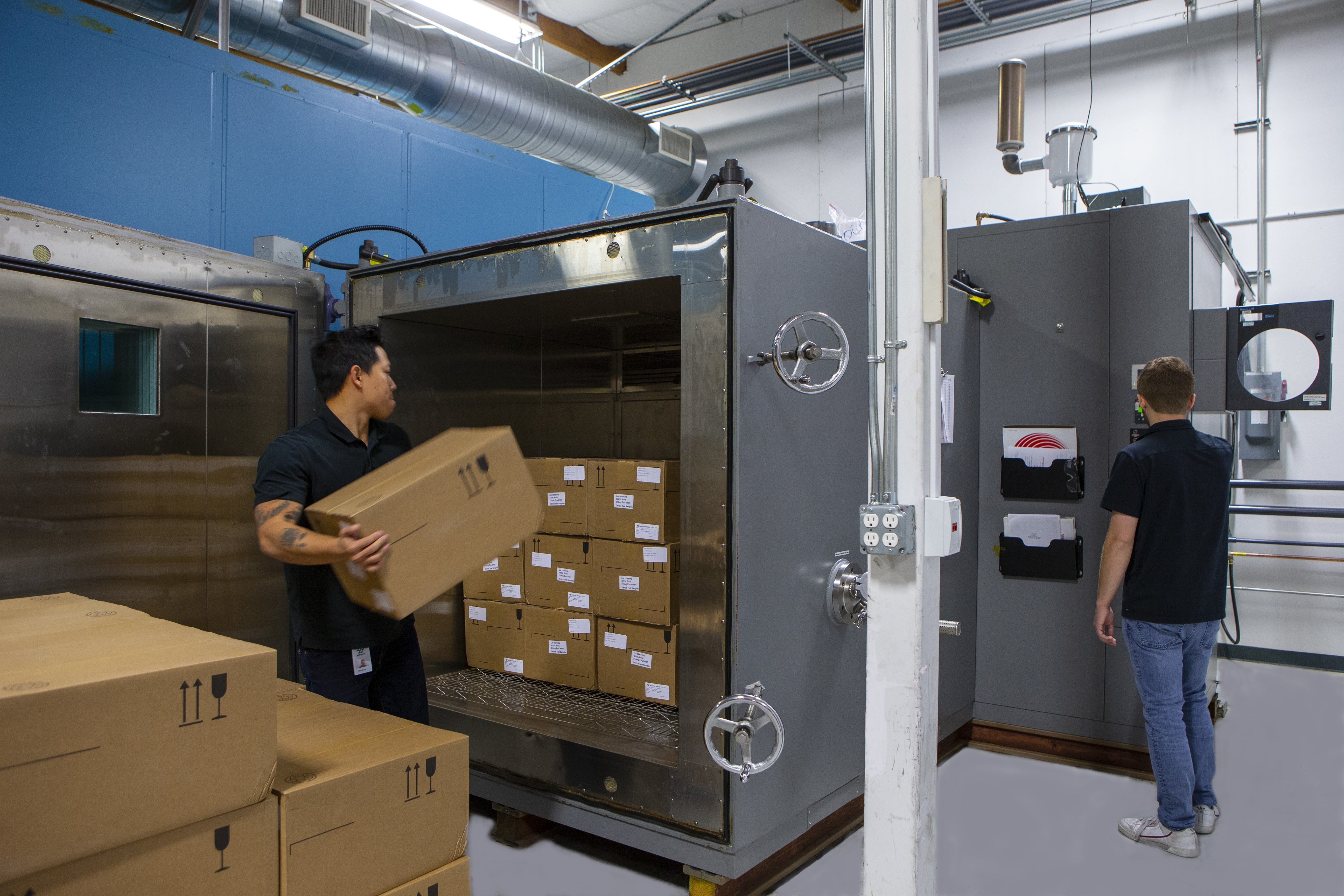
Internal Pressure
Hazmat test specifications require that any sealed vessel be subjected to a pressure differential test equal to one atmosphere.
The test is designed to guarantee that packages subject to high temperatures and/or lower external pressures (higher altitude) will not leak or explode. Testing can be conducted by means of internal pressurization of the package system or by means of drawing a vacuum in the area immediately surrounding the sealed container. The internal pressurization method is often favored because of its ability to determine the margin of safety built into a given package design.
Typical Procedures/Protocols
49-CFR 173.27c
WESTPAK Capabilities
(6) Vacuum chambers – various sizes; Large assortment of pumps, piping, and other equipment necessary for this test.
Vibration
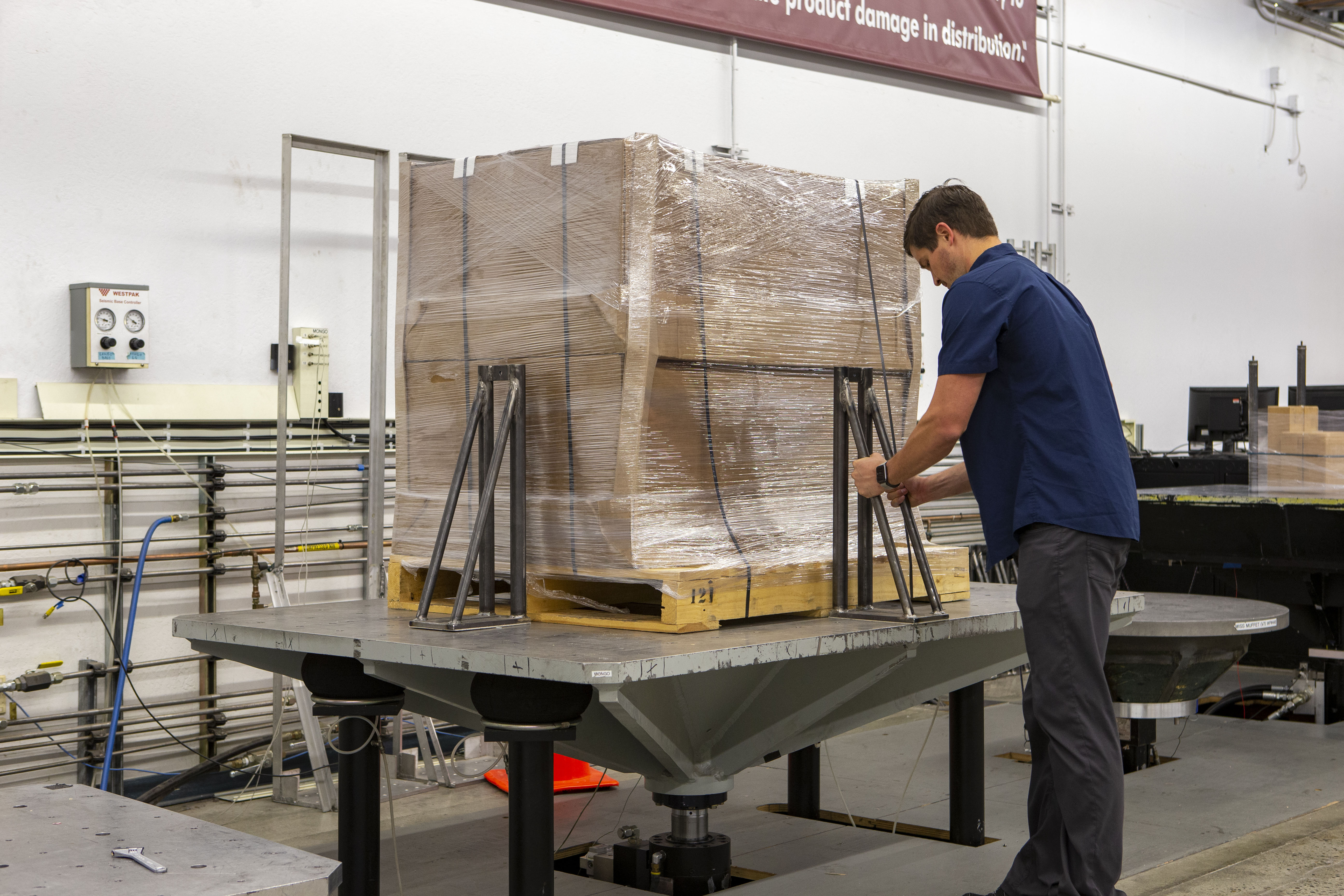
Vibration
Although not required, Westpak recommends that vibration testing be conducted in order to verify the ability of packaging to properly protect the product given that vibration is a certainty in the distribution environment.
There are two types of vibration testing that comply with the 49 CFR 179.608 Standard. One type, ASTM D999, utilizes a mechanical vibration test machine with a fixed 1 inch displacement and a circular synchronous motion when viewed from the side. This procedure is often referred to as a mechanical bounce test in that the package must be allowed to leave the surface of the vibration machine. The second procedure or type of vibration utilizes electrohydraulic or electrodynamic vibration test equipment with a random vibration profile typical of ASTM D4728 or similar.
Utilizing either procedure, it is important to replicate vibration that occurs in the real world to the product or package system under test in order to witness the effects and identify weaknesses. Vibration occurs on all forms of transportation and at varying levels of intensity. Real world vibration is complex and can intensify the natural frequency responses within a product/package system.
Typical Procedures/Protocols
49-CFR 178.608
WESTPAK Capabilities
Westpak continually upgrades and expands its equipment line-up. Therefore this list is a minimum of our capabilities:
(3) Horizontal Vibration Tables
(12) Vertical Vibration Test Systems with frequency ranges of 1-2000 Hz and load capacities to 1,500 kg (3,300 lb.)