Gross Leak Test (Bubble Test)
The Gross Leak Test is used to locate leaks in a tray and pouch pack systems, which can jeopardize the sterility of the product inside. Bubble leak testing is conducted by submerging the package one inch below the surface of the water and then pressurizing. Once the product packaging system has been submerged, operators observe the package to see if there are any steady streams bubbles rising to the surface. The presence of a steady stream of bubbles indicates that air or gas has escaped from the package system, and thus a leak is present.
What is the purpose of gross leak and bubble testing?
Bubble testing is a widely used qualitative method of determining defects or gross leaks in sterile medical device packaging. Primary packages or Sterile Barrier Systems are subjected to this test to determine if their ability to maintain a sterile barrier has been compromised by tears, holes, or improper seals. When properly applied in a package validation test plan (within guidelines of ISO 11607), this method has significant advantages to methods such as dye penetration testing when determining if a Sterile Barrier System has been compromised.
Bubble testing is the most common method used to determine the ability of a package to maintain a sterile barrier since it tests the entire Sterile Barrier System and not only the seal. Whether or not a product packaging system can maintain a sterile barrier is particularly important when it comes to the medical device industry. A compromised sterile barrier can lead to contamination and at a minimum render the product inside the packaging unusable, and may risk patient safety.
With the data gathered from bubble leak testing, manufacturers and designers can find leaks and pinpoint vulnerabilities in their product packaging system. They can then use this information to improve their package system and minimize the risk of their products becoming contaminated while in transit. When a medical device manufacturer optimizes a product’s Sterile Barrier System, this can lead to greater profits, higher customer satisfaction, and an increased level of safety for consumers.
Typical procedures and protocols of bubble testing
The typical procedures and protocols that WESTPAK is capable of employing for its bubble emission testing include:
- ASTM F2096
While we continually update existing testing equipment and acquire new technology, our labs currently have four bubble leak tanks with state-of-the-art controls that we use to conduct bubble testing.
How is a bubble test performed?
The ASTM F2096 test method requires a number of steps in order to properly execute a bubble leak testing procedure. Below, we’ve outlined the general steps required to complete a bubble testing procedure:
- Inflate the sample package underwater to a predetermined pressure
- Visually observe the sample package and look for any air bubbles
- Record whether air bubbles emerged from the sample package
- If there is a steady stream of bubbles circle the location of the bubbles for further analysis.
ASTM F2096 is a destructive test method that brings about a pass or fail result. Failure is indicated by a steady stream of air bubbles emerging from the packaging system and rising to the water’s surface. Different industries may allow for different levels of leakage in a product packaging system. However, when it comes to medical device manufacturing, pouches and packages should typically exhibit no leakage whatsoever.
Bubble testing can also be altered by adjusting the method of pressurization and the level of pressure the sample package is exposed to. High pressure tends to increase the sensitivity of the results, while low pressure reduces sensitivity. Before testing, it’s important to establish the minimum test pressure so that repeatable and accurate results can be achieved.
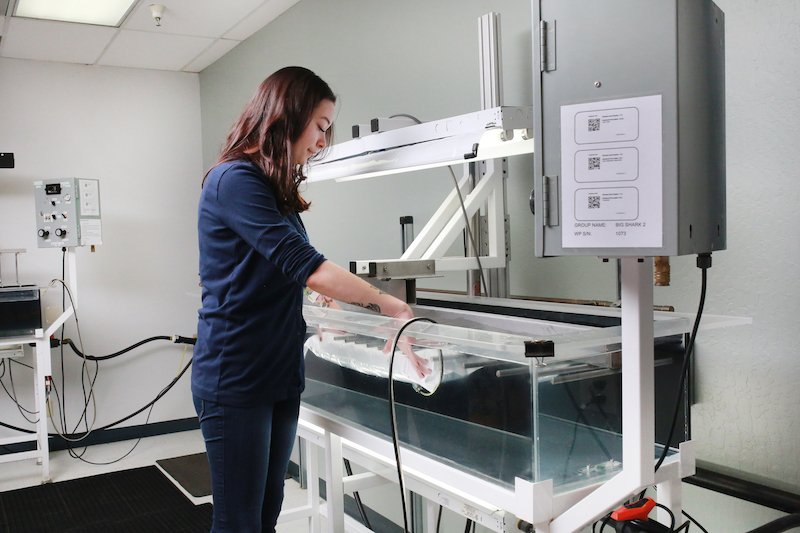
What are the advantages of bubble emission testing?
Gross leak testing (Bubble Testing) is such a common testing method in large part because it offers many advantages to manufacturers and engineers alike. Below, we’ve highlighted some of the primary advantages of bubble testing:
- Affordable: When compared to other product packaging tests, bubble testing is extremely affordable. It’s a cost-effective way to evaluate the integrity of a product packaging system.
- Quick: Test packages take little time to prepare and the test itself is very quick. If a leak exists in the product packaging system, bubbles will typically start to emerge within seconds of inflating the sample package.
- Simple: bubble testing is a straightforward process that can be carried out with relatively basic equipment.
- Versatile: bubble testing can be used on a wide range of different packaging systems. Whether you intend to test a box, a bottle, a pouch, or some other package, a bubble test can get the job done.
At WESTPAK, we have a team of engineers who are experienced in conducting bubble testing on a wide array of product packaging systems. We can run gross leak tests and provide you with recommendations for how to strengthen the integrity of your product packaging system. Contact us today to schedule bubble testing for your particular packaging system.
WESTPAK Capabilities
(8) Bubble Leak tanks with state-of-the-art controls
Accreditations:
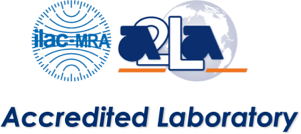
Testing at WESTPAK has been accredited by A2LA to comply with ISO 17025.
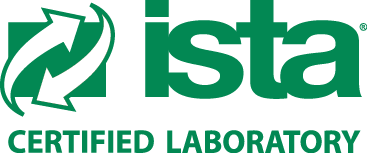
WESTPAK testing labs are ISTA certified to perform a variety of tests.