Vibration Testing
Vibration testing examines a product’s response to vibration as well as how a packaging system positively and adversely contributes to the transportation, handling, and preservation of the product.
Vibration & Resonance Testing
Vibration testing is a form of reliability testing that evaluates the product’s response to a defined vibration environment. Vibration testing specifically examines how a product and its packaging respond to different vibration inputs that may occur over the course of its lifetime. By exposing products to this input, vibration testing can help detect potential vulnerabilities and performance defects before the product goes into production or distribution.
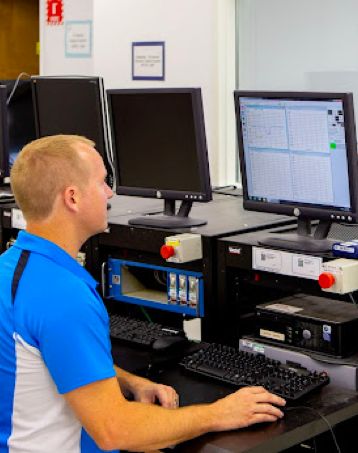
Purpose of conducting a vibration test
The purpose of vibration testing is to study how a product will respond to a variety of conditions that it may face in shipment or in-use environments.
Through vibration and resonance testing, Westpak provides important data that enable design teams to:
- Find their product’s natural resonance frequencies
- Identify gaps and vulnerabilities in the mechanical design
- Identify appropriate packaging solutions for safe transportation
- Determine the effect of the transportation environment and protective package system on the product
- Assess how a product will respond to vibration in the in-use environment
- Gain useful insight into distribution and user environments to prevent costly damage
Importance of Vibration Testing
Vibration occurs in all modes of transportation and in varying degrees of severity. Vibration is much more complex in the real world, and it can trigger a product’s own natural frequencies, causing rapid degradation and, in some cases, product failure. The package can be designed to attenuate this resonance and protect the product from vibration damage.
Vibration testing not only examines a product’s response to vibration, but it also tests how a packaging system positively and adversely contributes to the transportation, handling, and preservation of the product. Because a package system’s cushioning has its own frequency response, it may interfere with and, ultimately, prove detrimental to the contents. If the product and package’s natural frequencies are the same, for example, the resonance will amplify and damage is likely to occur.
To properly design a package where the cushion system attenuates the natural resonance of the product, vibration testing on both the product and package system should be conducted. Data-driven decisions can be made from these results.
What are typical vibration testing standards and protocols?
There are several vibration testing standards set forth by ASTM, IEC, ISO, and MIL STD.
Westpak lab facilities are equipped to perform a variety of vibration testing methods. Vibration inputs are the one guaranteed element of the distribution cycle. Therefore, all types of products should be considered for vibration testing.
Protocols
- ASTM D3580
- ASTM D4728
- ASTM D5112
- IEC 60068-2-6
- IEC 60068-2-64
- ISO 2247
- ISO 8318
- MIL STD 167
- MIL STD 810G
- MIL STD 883
Common Products
- Electronics and networking equipment
- Data storage racks
- Cell phones and consumer devices
- Biomedical and surgical equipment
- Military equipment
- Aerospace equipment
- Food products
- Vehicles
Capabilities
(10) Electro-Hydraulic Shakers
(9) Electro-Dynamic Shakers
Frequently Asked Questions
Get answers to our most frequently asked questions.
How are vibrations simulated during a vibration test?
Our accredited lab facilities conduct a variety of simulations to test the relationship between a product and its packaging to vibration inputs encountered in transit, handling, and in-use environments. Our laboratories utilize electro-hydraulic and electro-dynamic shakers to reproduce the vibration inputs encountered.
The vibration machine controllers may be programmed to deliver a variety of vibration inputs including:
- Shock and bounce (i.e., during transportation)
- Free-fall
- Random shocks
- Sinusoidal vibration
- Resonance Search & Dwell
- Narrow Band or Random-on-Random
- Sine-on-Random
- Combined Temperature and Vibration
- Combined Vibration, Cold Temperature, and Altitude
What environments do the vibration testing methods simulate?
Vibration inputs can have an effect on the product, cushion system and package system. It is therefore one of the most important inputs to study and mitigate against. The product itself will have a natural resonance that may be amplified during its course of travel.
When the product – together with its cushion and package system – enters the distribution process, it travels through a series of steps before arriving at its final destination. During distribution, a product is packaged, transported via land, sea, or air freight, and handled by individuals and a suite of equipment along the way. Within these environments, products will likely encounter different levels of shock and vibration that may negatively impact the integrity of the product.
Through vibration testing, Westpak can simulate the various environments and modes of transportation that a product and its packaging may be exposed to, therefore giving a higher probability of successful transit.
Our goal is to provide the best customer experience possible, as well as accurate, dependable reports produced by calibrated, tested, and well-maintained equipment by qualified personnel who follow Good Laboratory Practices. Through ISO accreditation and ISTA certification, Westpak is proud of our commitment to excellence.
Accreditations:
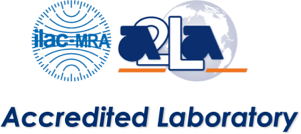
Testing at Westpak has been accredited by A2LA to comply with ISO 17025.
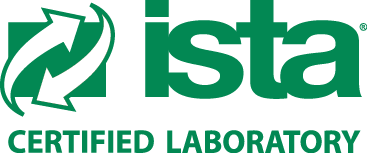
Westpak testing labs are ISTA certified to perform a variety of tests.