Package Testing
Package testing is utilized to determine if a package system will effectively protect the products through to its final destination by its simulating distribution environment.
Package Testing
When delivering goods to a customer, the products must arrive at their destination safely and without damage. Broken products, contaminations, and spills can compromise patient safety, disappoint the customer, lower profitability, and ultimately lead to the loss of future sales. One of the best ways to ensure that a product arrives at the end-user safely is to utilize a correctly designed and tested package system; this will ensure that the contents are protected as they move through the transportation distribution environment. First, however, we must test a package system to know how effective it is. Here, we will define what a package system is and explore what makes package testing so essential.
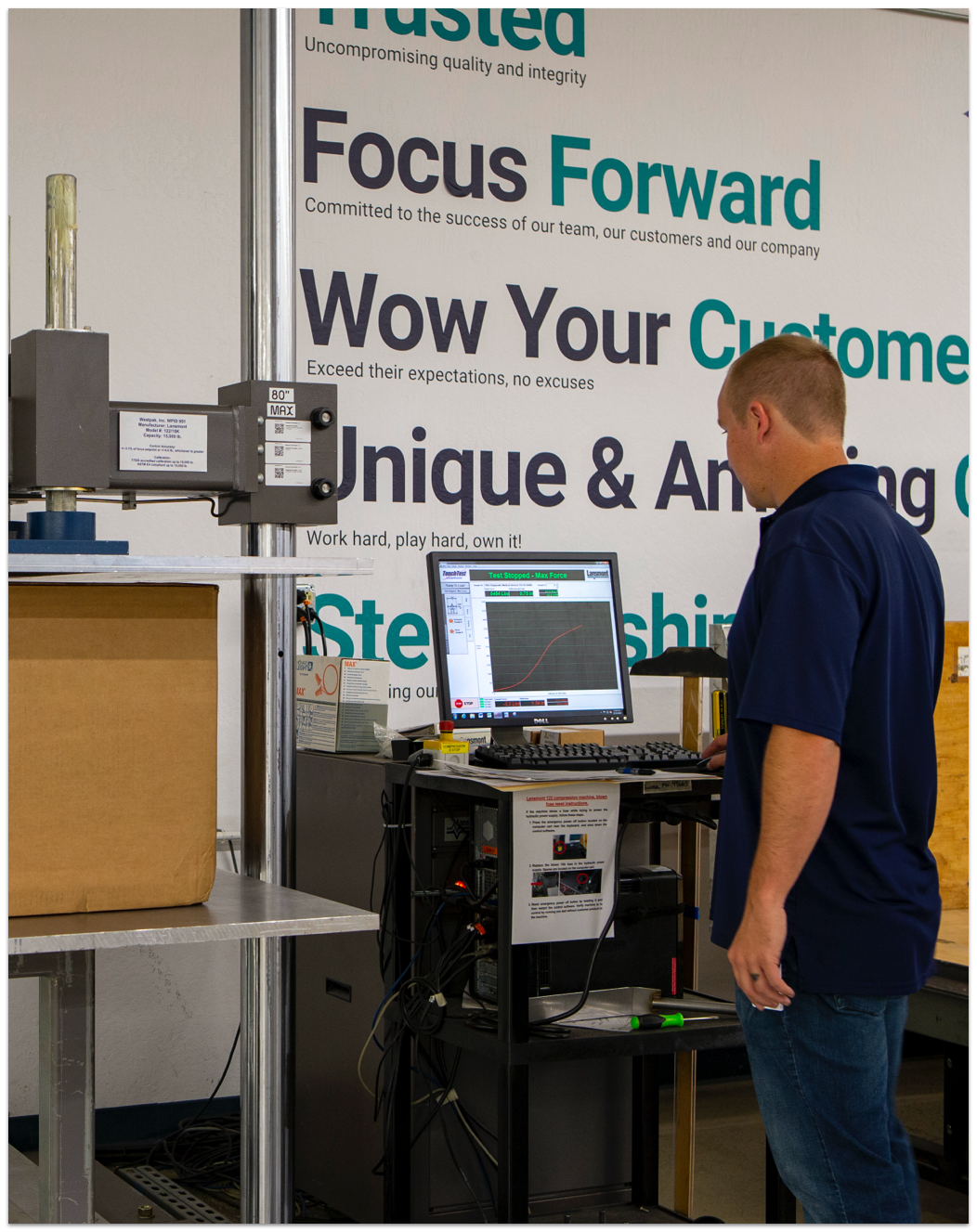
What Is a Package System?
A package system refers to the physical materials and containers that secure and protect the product as it moves through the distribution environment. Whether the package contains a lifesaving medical device, a temperature controlled pharmaceutical, food products or consumer goods, everything must pass through it. All products have an innate robustness and a point at which they break. The packaging system – whether it’s boxes – bottles, cans, or containers – is the great equalizer; its job is to supplement the product’s robustness and ensure it is successfully delivered to the end-user safely and without damage.
What types of packaging testing methods are there?
In many cases, products are overpackaged, resulting in excessive costs and environmental waste. Conversely, under-packaging can lead to excessive product damage and harm to the brand reputation. An optimized package system takes into account the ruggedness, strength, and durability of a given product, resulting in packaging that is both functional and cost-effective. In the end, the product should have just enough packaging to provide protection from the point of manufacture to the point of end use. When packaging systems are optimized and proper design is employed, a synergy emerges between the product and package.
Westpak employs a number of cutting-edge methods when it comes to package testing. We commonly test packages using methods such as:
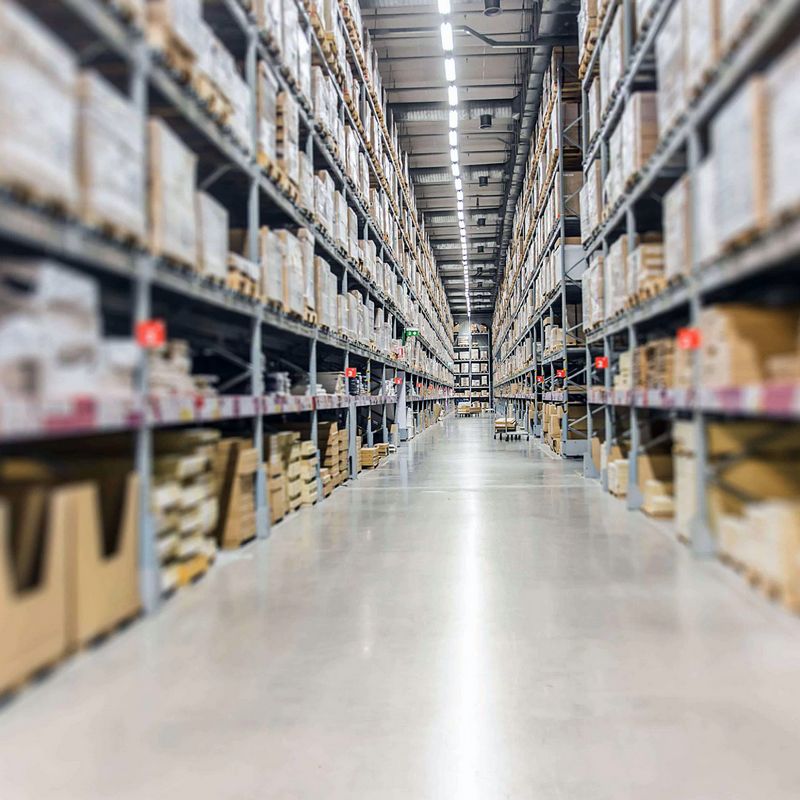
Amazon package testing
Westpak is a member of Amazon's Packaging Support and Supplier Network (APASS) and approved to test and certify products as Amazon Prep-Free Packaging (PFP), Ships-In-Own-Container (SIOC), and Frustration-Free Packaging (FFP) for vendors, sellers, and manufacturers.
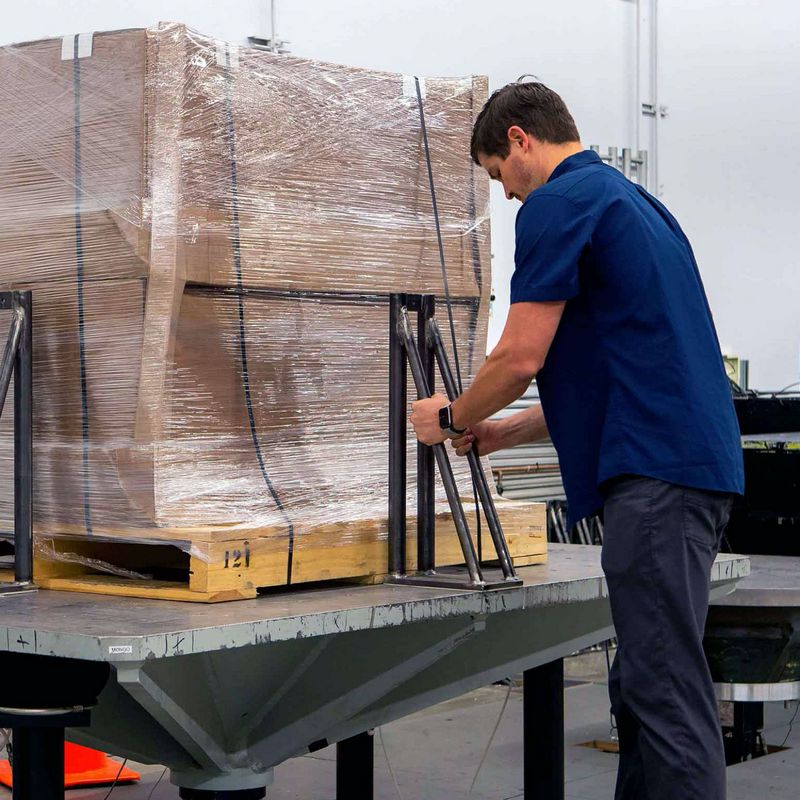
Distribution testing
Distribution testing is the practice of conducting tests that simulate the distribution environment in a laboratory. Lab testing provides a controlled and repeatable setting where the packages can be evaluated. ASTM and ISTA standards are the most frequently referenced standards.
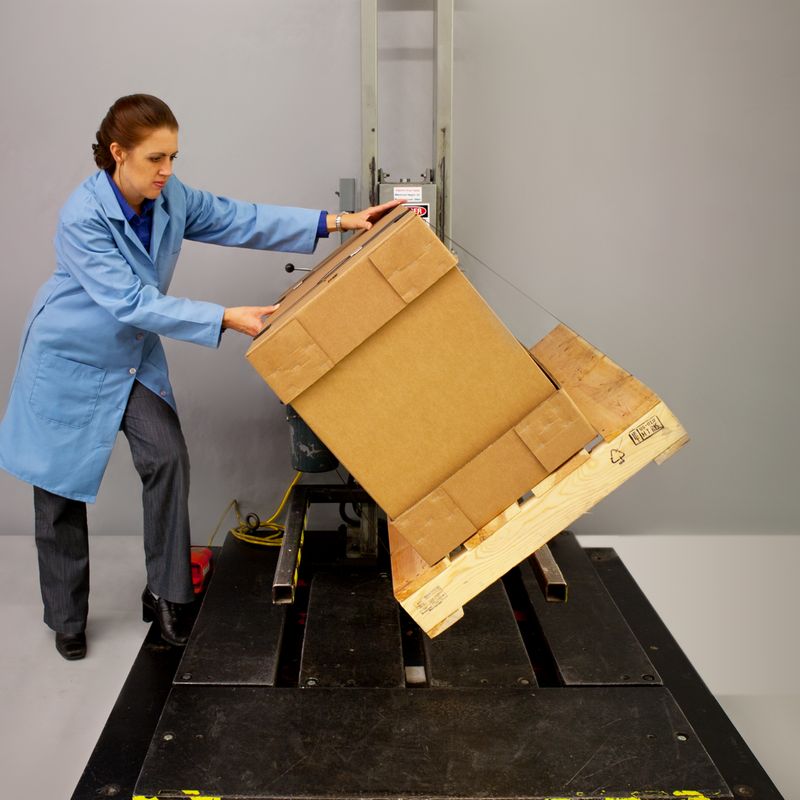
Drop testing
Our trained operators use specialized drop testing machines to evaluate a package system's ability to protect the product from impacts occurring in the distribution environment. Items ranging from small parcels to large crates can be repeatedly and consistently dropped from several feet to a few inches onto various surfaces.
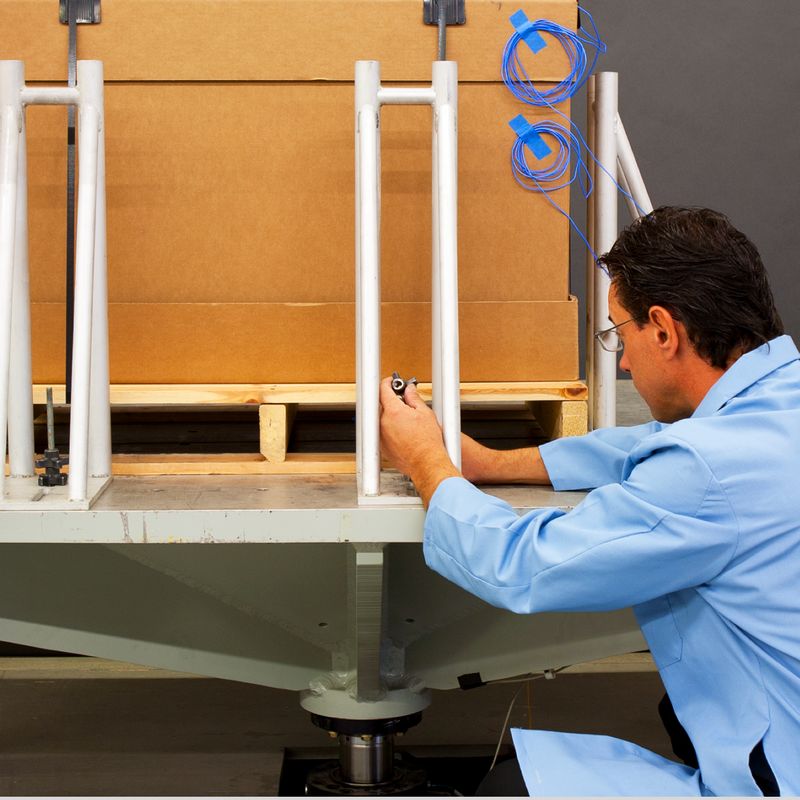
Vibration testing
Using vibration test machines and spectra from industry standards, packages and products are subjected to vibration testing that simulates truck, rail and air shipments.
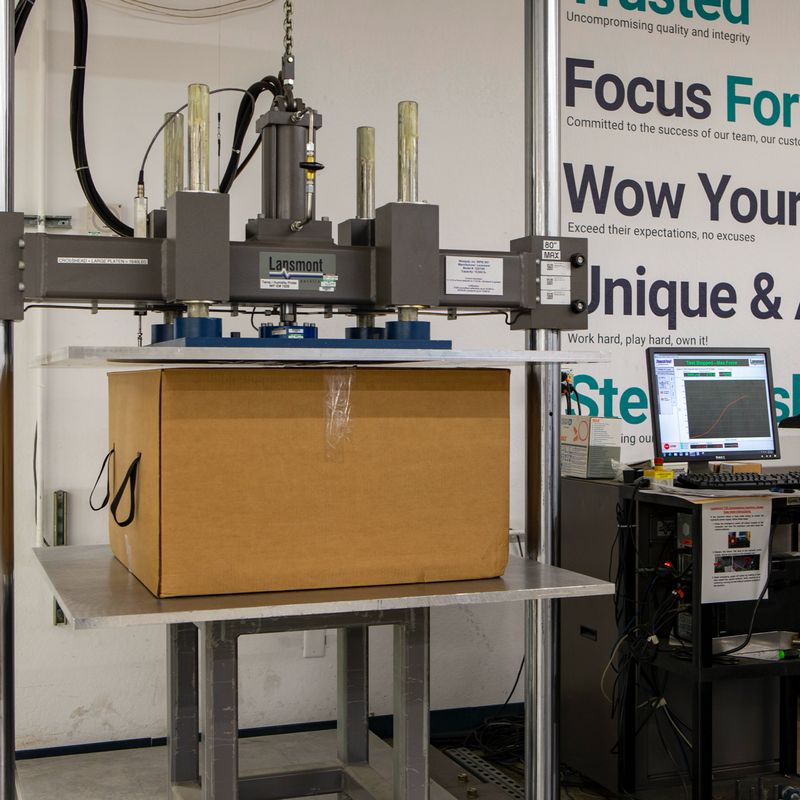
Compression testing
Compression testing simulates the effect of a package being stacked during transportation and storage. A package on the bottom of the stack will experience more compression force than a package at the top of the stack. This test input can also be combined with vibration testing.
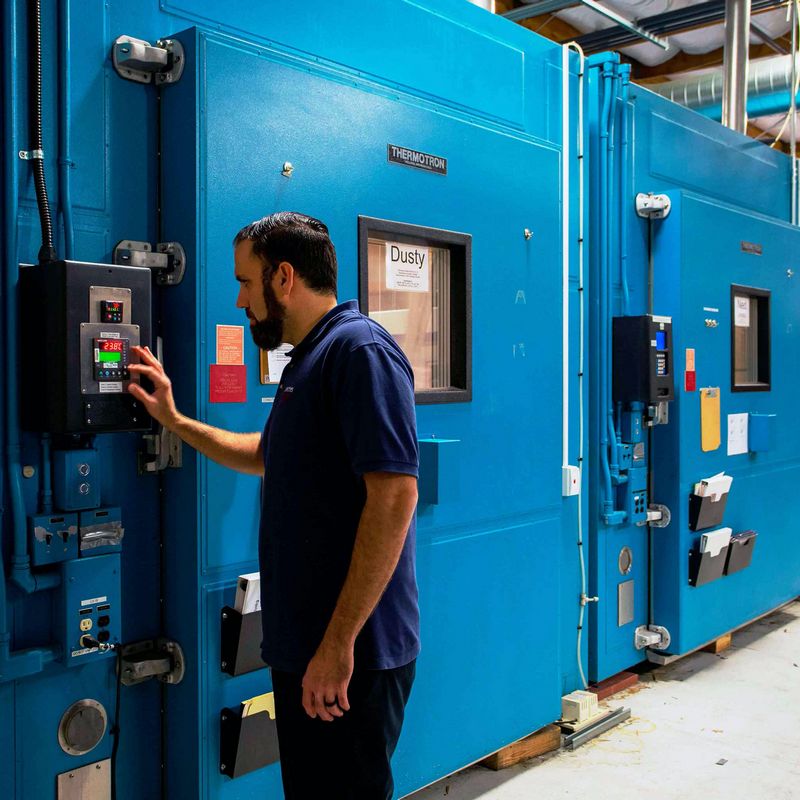
Environmental Conditioning
One of the first test processes often required prior to conducting physical testing on the package or container is environmental conditioning. This process subjects the packages to pre-determined environments stimulating, for example, desert, tropical and frozen environments.
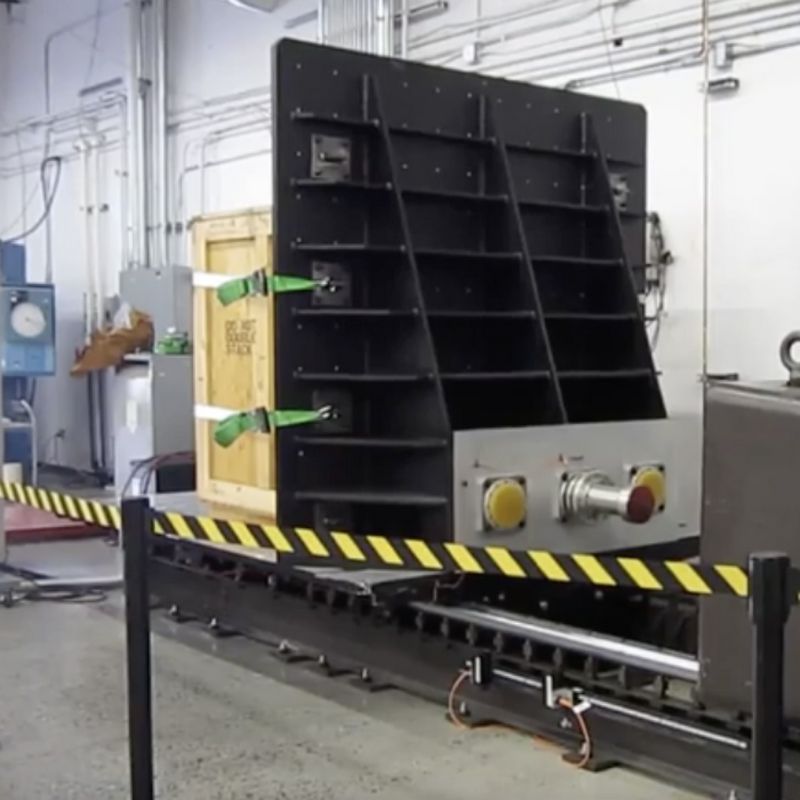
Horizontal impact testing
Westpak's Horizontal Impact Test System (HITS) primarily tests products and package systems for damage resistance due to railcar coupling. However, this versatile system also tests for sensitivities to other types of horizontal impacts including rough forklift handling and truck docking. Testing with the HITS is also beneficial for heavy or oversized products requiring shocks in all orientations.

Incline impact testing
One of the most utilized pieces of shock test equipment in package testing is the incline impact or Conbur tester. The specialized machine evaluates the ability of the packaging system to withstand crushing forces or sudden impacts.
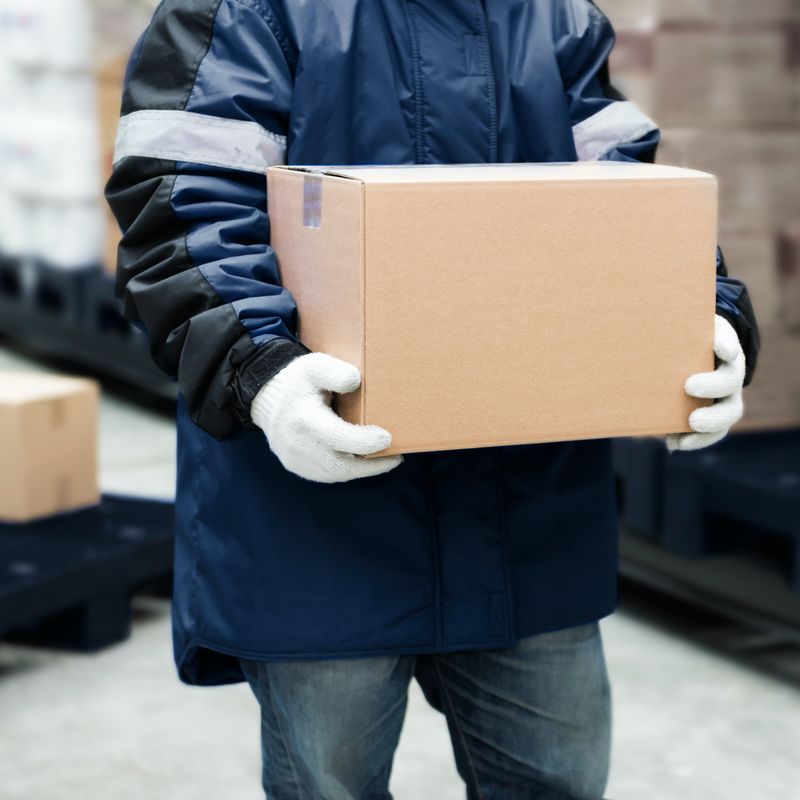
Cold chain testing
Testing that evaluates a package system's ability to withstand a temperature-controlled supply chain.
Frequently Asked Questions
Get answers to our most frequently asked questions.
What conditions are tested during package testing?
To gauge the ruggedness and durability of a particular package, it must be exposed to different conditions within a laboratory setting. Some of the conditions that Westpak conducts package testing for include:
- Freefall drop and shock
- Vibration
- Concentrated impacts
- Compression (vehicle and warehouse)
- Incline impact
- Temperature and humidity inputs
- High and low pressure (altitude) inputs
- Loose load / mechanical bounce
- Rough forklift handling
What are the common packaging test standards?
Our team follows the procedures and packaging test standards set forth by organizations such as ASTM and ISTA, both of which publish technical standards that are used by individuals and companies around the world. We are also happy to both develop and run custom protocols tailored to your specific needs.
Some of the typical procedures and protocols we practice when testing packages in our lab include:
- ISTA 2A, ISTA 2B
- ISTA 3A
- ISTA 3B
- ASTM D4169
- ASTM D4332
- ASTM D642
- ASTM D4728
- ASTM D5276
- ASTM D6055
- ASTM D6653
- ASTM D3103
- ASTM F2825
- ASTM D4003
- ASTM D880
- ISO 2233
Why Should I Conduct Package Testing?
Package testing helps you to determine if the package system will effectively protect the products through to its final destination. Testing simulates the distribution environment. What does a package experience in the back of a delivery truck? How does it react when placed at the bottom of a mixed-load stack? How do temperature and humidity inputs of different climates affect the packaging? These questions are answered through distribution testing. When it comes to sterile packaging for medical devices and pharmaceuticals, the importance of package testing cannot be understated. Package testing gives you a high degree of confidence in the efficacy of your package design.
Accreditations:
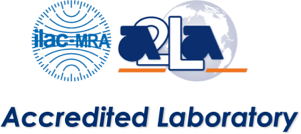
Testing at Westpak has been accredited by A2LA to comply with ISO 17025.
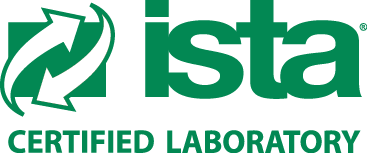
Westpak testing labs are ISTA certified to perform a variety of tests.