Thermal Shock Test
Thermal shock testing subjects packaging systems to elevated temperatures to evaluate the stress and shifts that occur within package contents.
Thermal Shock
Thermal shock testing exposes products to rapidly alternating low and high air temperatures. These temperature changes can be extreme, sometimes reaching highs of 200° C and lows of -80° C. When subjected to extreme temperatures, objects can experience significant stress and shifts in their integrity and performance.
Thermal shock tests are a tool manufacturers can use in order to analyze a test sample’s vulnerabilities to rapid, repetitive temperature changes in distribution or transit settings. For example, electronic devices used in delivery trucks in the winter can be exposed to many cycles of thermal shock during a single day. Devices fastened to the fuselage of a commercial aircraft can be exposed to extremely wide fluctuations in temperature as well.
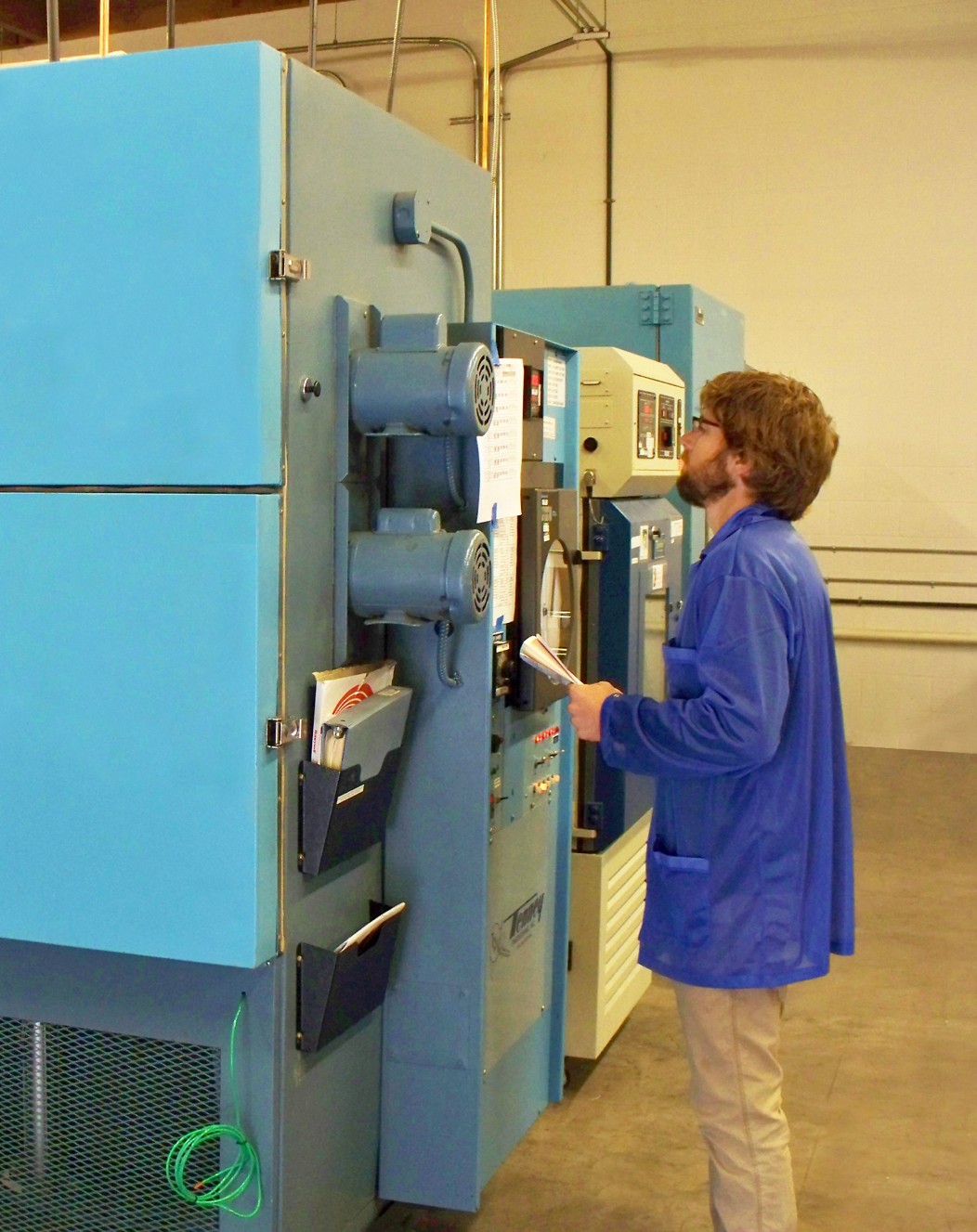
Purpose of Thermal Shock Testing
The purpose of thermal shock testing is to study how a manufactured object will react to extreme temperature changes that occur in their normal use environments, as well as distribution or transit environments. Intense thermal shocks are common in these settings but may compromise a product’s performance.
For example, thermal shocks may cause a product to:
- Shatter
- Bind
- Crack
- Experience damage to internal components
In order to avoid these issues and develop quality, robust goods, it is critical for manufacturers to understand the level of temperature change their product can withstand. Thermal shock testing is one reliability test that can do this.
Frequently Asked Questions
Get answers to our most frequently asked questions.
What are the typical protocols used for thermal shock testing?
Thermal shock testing can be customized depending on the product you’re testing; our team can help you identify the parameters that are best suited to the product or application.
Some examples of typical protocols used for thermal shock testing include:
- IEC 60068-2-14
- MIL STD 810G
At what temperatures are thermal shock tests performed?
Thermal shock tests employ a wide range of high and low temperatures in order to understand an object’s response to extreme environmental changes. Typically, thermal shock tests range between 200° C and -80° C.
How is a thermal shock test performed?
Thermal shock testing is performed in an environmental chamber with built-in cooling and heating mechanisms. The test sample is placed within the chamber and is repeatedly exposed to rapidly and aggressively changing temperatures. As the procedure continues, observations regarding the sample’s performance and appearance are reported.
Once this data has been collected, the thermal shock testing lab can report metrics to the customer, who can identify and address weaknesses exposed during testing.
What industries can benefit from thermal shock testing?
Any object that is transported as part of a distribution process can benefit from thermal shock testing. During transit and storage, a product may be exposed to a number of unique temperatures and environments. A product traveling across the United States, for example, may encounter cold mountain temperatures, hot deserts, and humidity throughout its journey.
Once this data has been collected, the thermal shock testing lab can report metrics to the customer, who can identify and address weaknesses exposed during testing.
Accreditations:
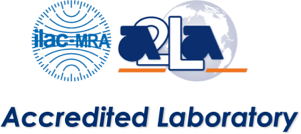
Testing at Westpak has been accredited by A2LA to comply with ISO 17025
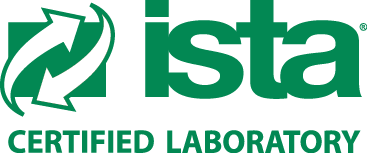
Westpak testing labs are ISTA certified to perform a variety of tests.