Temperature and Humidity Testing
Temperature and humidity testing subjects samples to various environmental conditions that may be encountered during transit, storage, and in-use environments.
Manufacturers must ensure that their goods can survive all of the environmental loads and strains they will face once they are introduced to production, transit, storage, and in-use environments. Temperature and humidity are two of the most important environmental factors that determine whether or not a product will still function optimally when in use. With temperature and humidity testing, manufacturers can obtain advanced insights into how an object will respond to the environmental conditions it will encounter throughout its lifecycle.
For example, medical device packaging is subjected to predetermined temperature and humidity conditions based on its distribution environment in preparation for package performance testing (i.e., compression, drop/impact, vibration). Environmental conditioning is necessary because paper-based materials, which are used in most packaging systems, experience degradation in physical properties as temperature and humidity change. Most plastic components change strength in direct proportion to changes in temperature.
What is the purpose of temperature and humidity testing?
From manufacturing to transit and delivery, packages and the products they carry may be exposed to a number of extreme environments. During shipment and storage, shipping containers, trucks, and warehouses are microclimates themselves, dependent on regional and ambient conditions.
When a package leaves the East Coast in winter, it may be subjected to cold, wet conditions en route to Florida’s warm, humid climate or the hot desert in Arizona. As it travels through these climates, the package and product may experience cosmetic or performance changes that alter its integrity.
Manufacturers can interpret how their product or package may react to various environmental conditions by conducting temperature and humidity testing. Armed with this information, they can identify and address potential vulnerabilities in their product and/or packaging system.
What are Westpak’s capabilities for temperature and humidity testing?
Our accredited lab facilities are equipped to perform a number of temperature and humidity testing procedures using:
- (65) Temperature and Humidity Chambers
- (4) Temperature and Altitude Chambers
- (1) Thermal Shock Chamber
Frequently Asked Questions
Get answers to our most frequently asked questions.
How is temperature testing performed?
Temperature testing employs controlled chambers that can quickly adjust temperatures by circulating hot or cold fluid through a closed loop through which internal chamber air passes.
When exposed to temperature changes, the performance and physical properties of a product may shift. By simulating these environments, manufacturers can better understand how their products will hold up in the real world.
How is temperature and humidity testing performed?
Similar to temperature testing, humidity testing also uses a controlled temperature and humidity chamber. Within the chamber, the temperature and humidity are programmed to represent similar environments the object may encounter in shipping, handling, and use environments. The environmental chamber is designed to maintain tight controls over both temperature and humidity, as well as the rates at which these factors are changed. The test levels chosen and rates of change between these levels are documented in the customer’s test report and encompass what might be encountered during the actual distribution cycle.
As the variables shift in a repeatable, controlled environment, the testing facility can report on changes to the testing sample. With these results, manufacturers can make more informed decisions regarding product design and packing conditions.
What products are suitable for temperature and humidity testing?
Temperature and humidity testing are valuable to a variety of industries, including medical, automotive, defense, aviation, energy, and telecommunication fields. Within these industries, humidity and temperature testing can be used on products such as:
- Medical devices
- Electrical components
- Engine assemblies
- Batteries and solar panels
- Adhesives and caulking
- Glazing products
- Medical diagnostic products
- Pharmaceutical containers
- Military munitions and weapons
Accreditations:
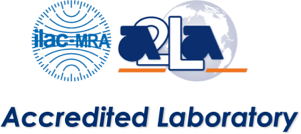
Testing at Westpak has been accredited by A2LA to comply with ISO 17025.
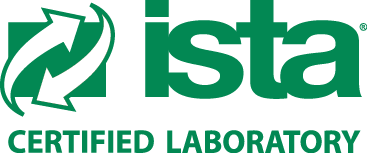
Westpak testing labs are ISTA certified to perform a variety of tests.